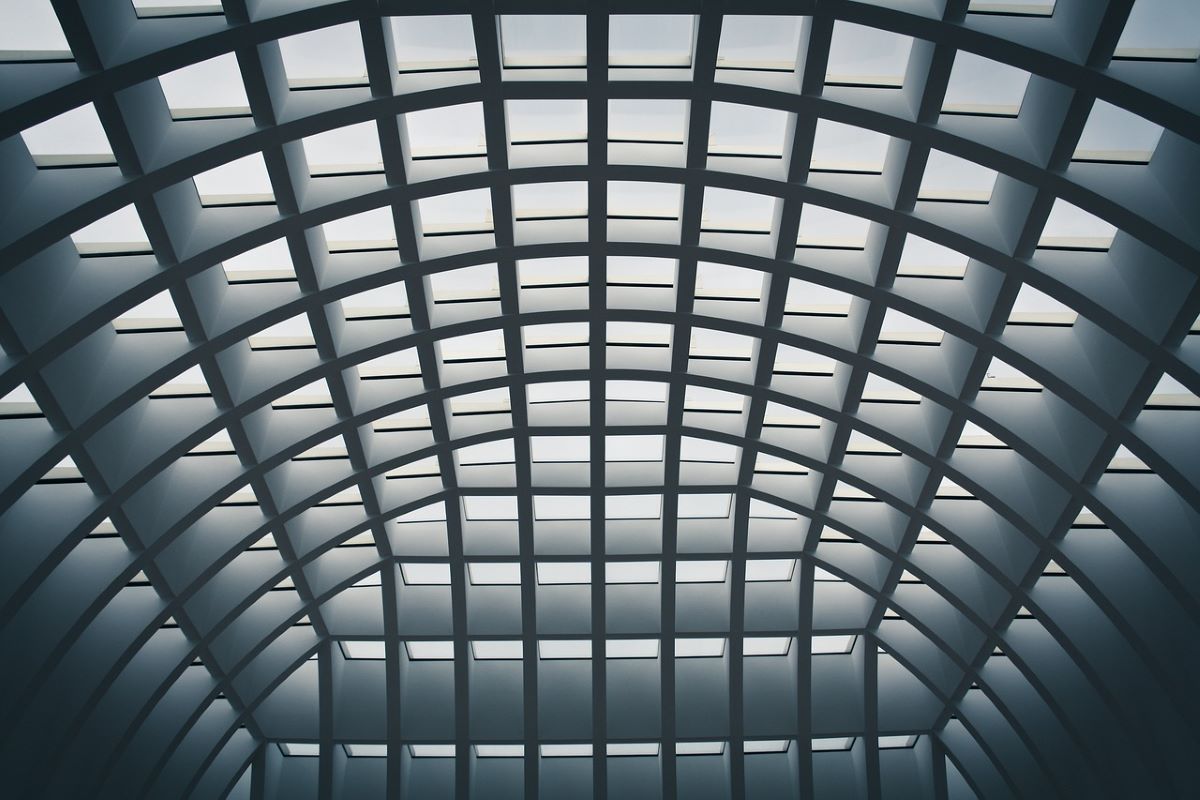
Constructing a building is a complex and expensive endeavour, with numerous variables that can impact the final cost. Keeping construction projects within budget is a paramount concern for developers, contractors, and stakeholders. However, cost control should not come at the expense of quality. In this comprehensive guide, we will explore five main areas that can help control construction costs without compromising on quality.
1) Detailed Planning and Design
Planning and design are extremely important to the success of any construction project. Rushing into construction without a well-defined plan can lead to costly changes, delays, and quality issues down the line. Here’s how to ensure a solid start:
Comprehensive Scope Definition
Begin by clearly defining the project’s scope, including objectives, specifications, and materials. Detailed drawings and specifications reduce ambiguity and make it easier to obtain accurate quotes from contractors.
Value Engineering
Value engineering involves optimising the project design to achieve the desired functionality and aesthetics while minimising costs. Experienced architects and engineers can suggest alternative materials or construction methods that meet project goals more efficiently.
Competitive Bidding
To control costs, solicit competitive bids from multiple contractors. Ensure that contractors provide detailed breakdowns of costs for labour, materials, and overhead. This helps you identify the most cost-effective option while maintaining quality standards.
2) Project Management and Communication
Efficient project management is essential for keeping construction costs in check and ensuring quality. Establishing clear communication channels among project stakeholders can prevent misunderstandings and costly errors.
Skilled Project Manager
Assign a qualified project manager who can oversee the construction process, manage resources, and coordinate activities. Their experience can help anticipate and mitigate potential budget overruns.
Regular Progress Meetings
Hold regular progress meetings with all stakeholders, including architects, engineers, contractors, and subcontractors. These meetings allow for real-time discussions of issues and changes, helping to prevent costly delays.
Change Order Management
Changes are inevitable during construction, but they can significantly impact the budget. Implement a strict change order management process to evaluate the cost and impact of changes before they are approved.
3) Material and Supplier Selection
The selection of construction materials and suppliers plays a crucial role in cost control and quality assurance. Consider these factors when making these critical decisions:
Material Quality vs. Cost
When considering materials for your construction project, striking the right balance between quality and cost is paramount. It’s essential to weigh the benefits of higher-quality materials against their associated expenses. Construction estimating services can assist in evaluating the cost implications of various material options, helping you make informed decisions. Leveraging building estimating techniques can also help in identifying areas where cost-effective alternatives can be incorporated without compromising the structural integrity or safety of the project.
Supplier Relationships
Develop strong relationships with suppliers and negotiate favourable terms. Bulk purchasing, discounts, and timely deliveries can reduce material costs without compromising quality.
Quality Assurance
Prioritise suppliers and manufacturers with a proven track record of delivering high-quality materials. Inspect and test materials as they arrive on-site to ensure they meet project specifications.
4) Efficient Construction Practices
Construction practices have a significant impact on both cost and quality. Employing efficient methods and technologies can streamline the construction process while maintaining high standards.
Lean Construction
Lean construction principles emphasise minimising waste, optimising resources, and improving productivity. Implementing lean practices can reduce project duration and costs.
Technology Integration
Leverage construction technology, such as Building Information Modeling (BIM) and project management software, to enhance communication, track progress, and identify potential cost-saving opportunities.
Skilled Labour
Hiring skilled and experienced labourers ensures work is done efficiently and correctly the first time. Skilled workers can prevent costly mistakes and rework, ultimately saving time and money.
5) Quality Control and Inspections
Maintaining quality standards throughout construction is crucial to avoid costly rework and repairs after project completion. Establish a robust quality control process:
Regular Inspections
Implement a schedule of regular inspections at key project milestones. Inspections should cover all aspects of construction, from structural integrity to finishing details.
Third-Party Assessments
Consider hiring third-party quality control experts to conduct independent assessments. Their objective evaluations can identify issues that might be overlooked internally.
Documentation
Thoroughly document all inspections, test results, and quality control processes. This documentation serves as a record of compliance with project specifications and can be invaluable in resolving disputes.
All in all, balancing construction costs with quality is an ongoing challenge in the industry. Always keep in mind that while cost control is essential, it should not overshadow the importance of safety and compliance with building codes and regulations. Cutting corners in these areas can lead to long-term liabilities and costly legal issues. By following the guidelines outlined in this guide, you can strike a balance between cost and quality, ensuring that your construction project is not only within budget but also meets or exceeds your expectations.
